Main Functions of WMS
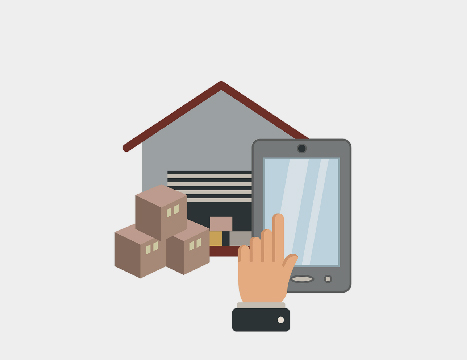
Real time inventory monitoring
The WMS system tracks inventory changes in real-time through barcode or RFID technology, ensuring data accuracy and timely updates.
Inventory optimization analysis
The system analyzes historical data, predicts inventory demand, helps managers optimize inventory levels, and reduces the risk of backlog and stockouts.
Automated replenishment process
The WMS system automatically triggers replenishment instructions based on inventory levels to ensure that inventory remains at its optimal level and improve response speed.
Inventory counting function
The system supports periodic or continuous inventory counting, reducing human errors and improving inventory accuracy through precise inventory counting functions.
WMS Multi Factor Login Method
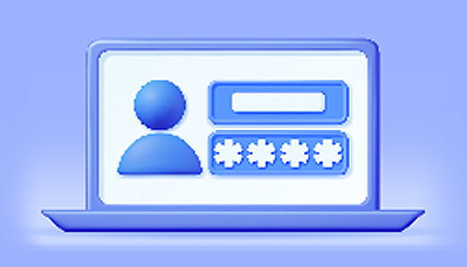
Password Login Mechanism
The WMS system provides a traditional password login method, where users need to enter a pre-set username and password combination, and only enter the system after verification.
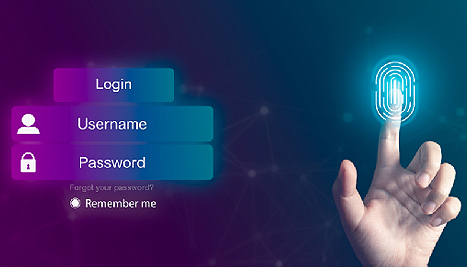
Fingerprint Login Technology
The system also supports advanced fingerprint login technology. Users can log in by touching the fingerprint recognizer, and the system will compare the fingerprint information with the fingerprint templates stored in the database. If the match is successful, the user can log in.
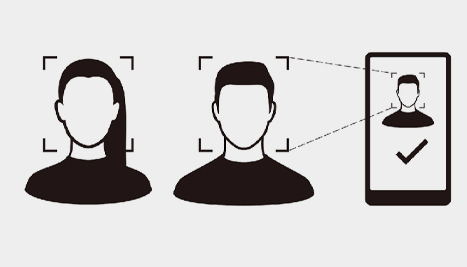
Facial Recognition Verification
In addition, the WMS system has introduced facial recognition verification function, which captures the user’s facial image through a camera and compares it with the registered facial data in the system to confirm the user’s identity.

Warehouse Management
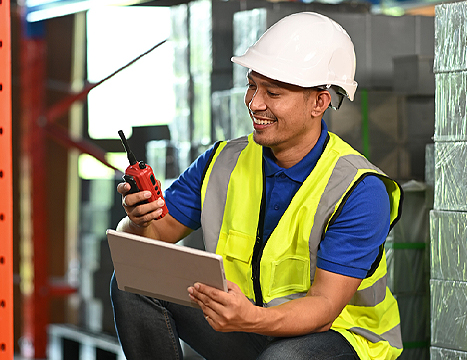
Fill in the inventory form
Select the product, fill in detailed information such as quantity, batch, production date, etc., and click “Confirm to add inventory form” to ensure that the data is correct.
Automatic processing by the system
After adding the inventory order, the document is automatically sent to the WCS system, notifying the system to start executing the inventory task.
Inventory management interface
Display the details and status of the inventory receipt, and query the inventory trajectory information based on conditions for easy tracking of operational status.
Operation reference manual
Please refer to the ‘Intelligent Warehouse Control System Operation Manual’ for detailed step-by-step guidance on specific operations.
Outbound Management
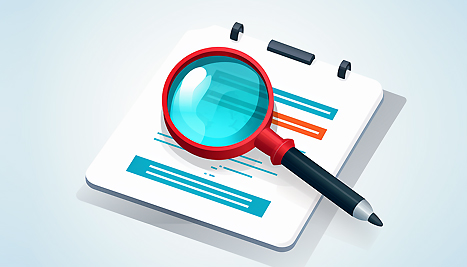
Entry of outbound order information
Select the product, fill in detailed information such as quantity, batch, and production date, and click [Confirm to add inventory form] to ensure that the data is correct.
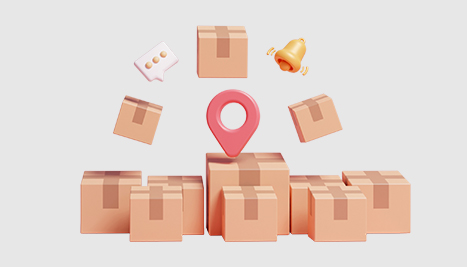
Tracking of warehouse receipt status
Display the details of the outbound order, update the status and trajectory information of the document in real time, and provide the function of querying the inbound trajectory according to conditions.
Inventory Management
Used to view detailed information of container inventory sheets, and can query inventory sheet information based on query criteria. As shown in the following figure.
Inventory ledger
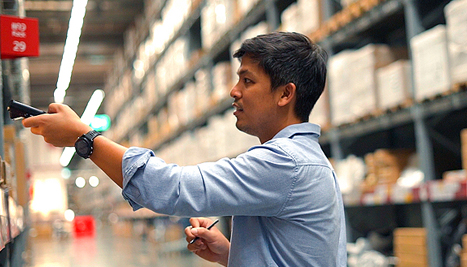
Container product inventory inquiry
Quickly view the inventory of each product, accurate to the specific container location, and the real-time inventory quantity is clear at a glance.
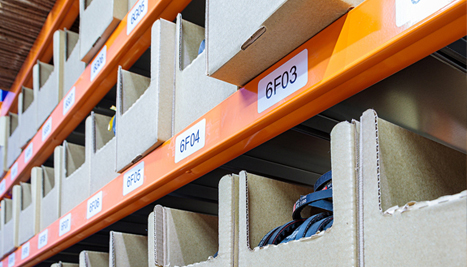
Detailed information of material inventory
Convenient retrieval of material inventory, display quantity, and precise positioning of materials in the container.
Basic Management
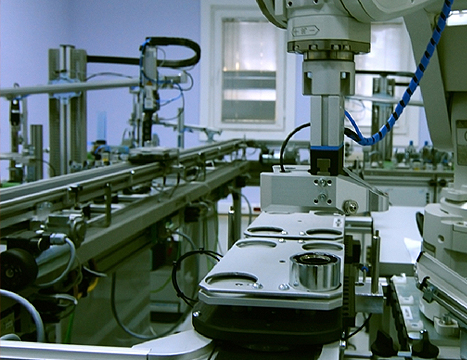
Material Information Management
Maintain material names, models, codes, barcodes, etc., support manual addition and import, and generate automatically without barcode system.
Material operation function
Add material names, codes, specifications, and models, which can be imported in batches and specified or deleted in batches.
Product information maintenance
Based on material management, maintain product information according to BOM combinations, including product specific information and inventory safety numbers.
Product operation function
New products are based on BOM combinations, and product information can be modified. Product deletion supports single or batch operations, and there is a confirmation prompt before deletion.
Equipment Management
01
Container Basic Information Management
Maintain factory default settings, including layout and box type. Once set, data cannot be changed.
02
Layout management and updates
The default layout is maintained by the manufacturer, and can be modified if the hopper design is adjusted. Layout, as the basic data, is not frequently changed after setting.
03
Storage settings and deletion
Configure the correspondence between products and pallet workstations to ensure correct storage. Storage settings that are no longer in use can be deleted.
04
Type and operation of material box
Define the classification and parameters of the material box, such as size, weight restrictions, etc. Provide modification and deletion functions to meet different storage requirements.
05
Box barcode management
Automated or manual management of material box barcodes, which can be automatically generated to ensure accurate tracking of information for each material box.
System Settings
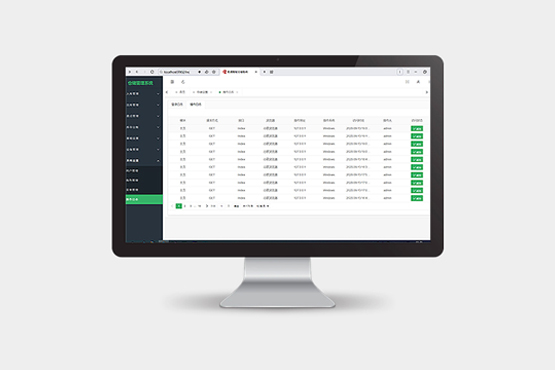
User Management
Add, delete, and modify users, add basic user information and set roles, delete users with confirmation prompts, and ensure safe operation.
Role permission settings
Manage roles and configure permissions, assign different functions to roles, and complete the authorization process through the authorization interface to ensure accurate permission allocation.
Operation log recording
Covering login logs and operation logs, detailing user behavior within the system for easy traceability and auditing.